December 21, 2017
Designing Products For The Value-based Medical Device Market
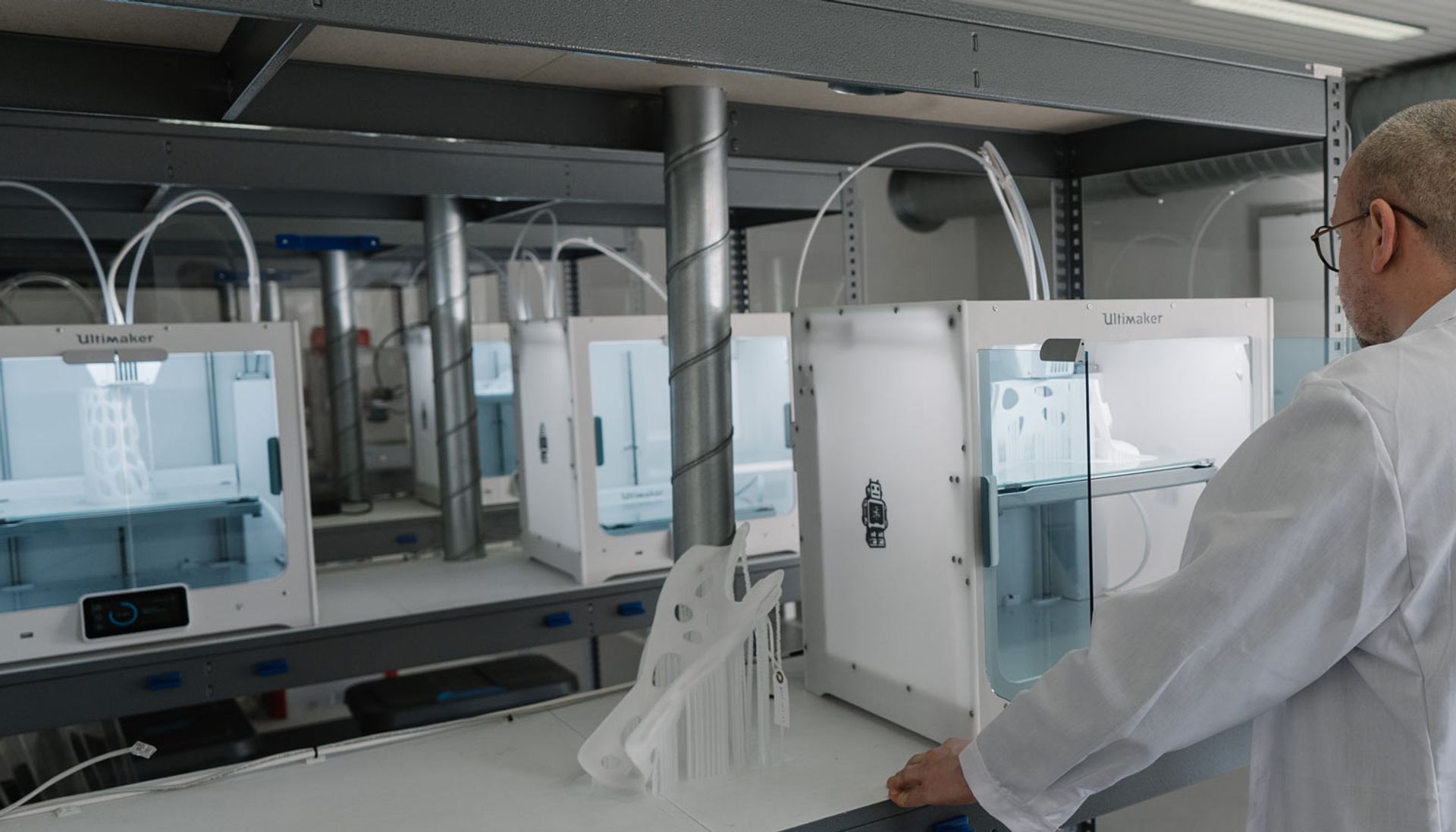
Orthopaedic device design is not always conducted with streamlined manufacturability and efficient operating room use in mind.
Todd Martens, Vice President of Product and Customer Development, Orthopaedic Implant Company 12.20.17 Orthopaedic device design is not always conducted with streamlined manufacturability and efficient operating room use in mind. Often, this leads to devices being far more expensive than their functional value would suggest. Complicating an implant system also results in requiring an abundance of support in the operating room and unnecessary tools that add to the length of a procedure and subsequent tray sterilization. All of this amounts to gratuitous costs for the hospital, and more importantly, for the patient.
Design for manufacturability (DFM) coupled with concurrent engineering aims to streamline manufacturing and shorten the product development time. Many device manufacturers consider DFM in later stages of the design process to “check the box” and get through a design review. Concurrent engineering in the medical device space requires cross-functional teams with representation from product development, marketing, manufacturing, and quality engineering. Incorporating both DFM and concurrent engineering in the initial stages of the design process, though often very challenging, can result in a product that is just as effective but exceptionally more efficient for production and use.
DFM and Concurrent Engineering Produces a Streamlined Equivalent
Orthopaedic Implant Company (OIC) relies on DFM coupled with concurrent engineering to help the company achieve its goals of bringing implants to market at the lowest possible prices. A great example of this is its recently released external fixation system. External fixation constructs are stabilizing fixation systems that often do not leave the hospital with the patient. They are put on to temporarily stabilize a fracture until definitive fixation is implanted. Despite their temporary nature, external fixation components are known for being the most expensive constructs across all orthopedic devices. Yet, the use of these proactive design methodologies has allowed OIC to reverse this trend.
OIC used DFM and concurrent engineering to create a simplified multipurpose clamp that provides either a bar-to-bar construct or bar-to-pin construct (see image). OIC also worked with contract manufacturers to minimize assembled parts and to utilize new machining technology to increase the speed of production. These proactive design methodologies required more collaboration and dedication of time to early stages in the process, but they have yielded a very cost effective and efficient external fixation system.
Beyond these product development-based processes, OIC utilizes other cost reducing strategies essential to the value-based care space. Each minute in an operating room (OR) costs between $60 to $120, and each additional person required to be in the OR to execute a device increases that cost too. Thus, to lower the overall cost of use, OIC tirelessly strives to optimize the layout of its sterilization trays. This intuitive organization and layout of implants and instruments, coupled with the minimization of superfluous instrumentation, increases the efficiency of their use in the OR.
Designing Products for the Value-Based Medical Device Market
OIC wanted to create a new model that would help hospitals and surgeons meet the performance requirements that value-based care is demanding. Adhering to the proactive design methodologies of DFM and concurrent engineering has helped OIC manufacture and sell implants proven to be clinically equivalent to premium-branded implants at a fraction of the cost. After consulting with surgeons, OIC worked with manufacturers from the beginning stages with a price target and efficiency model in mind.
OIC’s external fixation system is a great example of how the company has made DFM and concurrent engineering a cornerstone of its product development process. This new external fixation system will help round out OIC’s trauma portfolio as it continues to provide solutions for physicians and facilities in value-based and performance-based care.
Todd Martens has been working with orthopedic devices for 25 years, and has experience across the full spectrum of orthopedic disciplines, with a particular focus on trauma. His background combines engineering and sales management, giving him unique insight into the bridge between successful implant design and application. Martens joined Orthopaedic Implant Company in 2015 and his contributions to the organization have been tantamount to its success in fulfilling its mission of manufacturing the highest quality implants at the lowest possible prices.
Click here to see the article as published on the ODT website.